Accelerating the Shift to a Mobility Company

This presentation focuses on Toyota's efforts to transform itself into a mobility company.
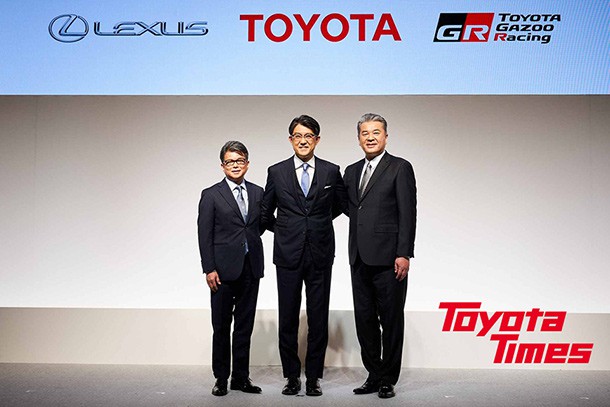

Accelerating the shift to a Mobility Company: President Sato Talks about Toyota's Future
The eyes of the world were on a recent briefing about Toyota's new management structure. There, new President Koji Sato explained the journey of transformation into a mobility company.
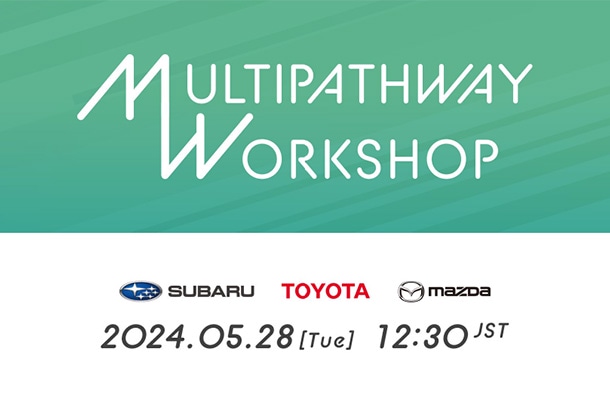
- Plug-in Hybrid
- Crown Signia
- Grand Highlander
- Land Cruiser
- Concept Vehicles
- Historic Vehicles
- 2025 Toyota 4Runner
- Los Angeles
- Global Shows
- What’s New for 2025
- What’s New for 2024
- What’s New for 2023
- What’s New for 2022
- Images & Videos
Latest News
- Sales & Financial
- Voluntary Recalls
- Takata Info
- Environmental
- Community Engagement
- Diversity & Inclusion
- Finance, Insurance & Banking
- Advanced Technology
- Research & Development
- Safety Technology
- Motorsports
- Company History
- Executive Bios
- Media Contacts
- Takata Recall

Toyota to Share Progress on Woven City at CES 2025
TOKYO (Dec. 17, 2024) ―Toyota Motor Corporation announces that it will return to CES 2025 with plans to make a presentation on Woven City during Media Days on January 6, 2025 starting at 1:00 p.m. Pacific Standard Time. The presentation will also be livestreamed, as outlined below.

CES 2025 Theme
- + Select All
- - DeSelect All

CES2025Theme-WovenCity
Email sign up.
Enter your email address below to sign up for email alerts.
* Indicates Required
Thank you for subscribing. Please check your email to validate your sign up.
You are already subscribed, your mailing lists have been updated.
Copyright Notice
All materials on this site are for editorial use only. The use of these materials for advertising, marketing or any other commercial purpose is prohibited. They may be cropped but not otherwise modified. To download these materials, you must agree to abide by these terms.
- Today's news
- Reviews and deals
- Climate change
- Newsletters
- Fall allergies
- Health news
- Mental health
- Sexual health
- Family health
- So mini ways
- Unapologetically
- Buying guides

Entertainment
- How to Watch
- My Portfolio
- Latest News
- Stock Market
- The Morning Brief
- Premium News
- Biden Economy
- Stocks: Most Actives
- Stocks: Gainers
- Stocks: Losers
- Trending Tickers
- World Indices
- US Treasury Bonds Rates
- Top Mutual Funds
- Options: Highest Open Interest
- Options: Highest Implied Volatility
- Basic Materials
- Communication Services
- Consumer Cyclical
- Consumer Defensive
- Financial Services
- Industrials
- Real Estate
- Stock Comparison
- Advanced Chart
- Currency Converter
- Investment Ideas
- Research Reports
- Credit Cards
- Student Loans
- Personal Loans
- Mortgage Calculator
- Editor's Picks
- Investing Insights
- Trending Stocks
- Morning Brief
- Opening Bid
- Streaming Now
- Fantasy football
- Pro Pick 'Em
- College Pick 'Em
- Fantasy baseball
- Fantasy hockey
- Fantasy basketball
- Download the app
- Daily fantasy
- Scores and schedules
- GameChannel
- World Baseball Classic
- Premier League
- CONCACAF League
- Champions League
- Motorsports
- Horse racing
New on Yahoo

Yahoo Finance
TOKYO , Dec. 16, 2024 /PRNewswire/ -- Toyota Motor Corporation announces that it will return to CES 2025 with plans to make a presentation on Woven City during Media Days on January 6, 2025 starting at 1:00 p.m. Pacific Standard Time . The presentation will also be livestreamed, as outlined below.
Presenting Toyota Executive: Akio Toyoda , Chairman of the Board of Directors (Representative Director)
Livestream* details Date/Time : Monday, January 6, 2025 , 13:00 p.m. (Pacific Standard Time) Tuesday, January 7, 2025 , 6:00 a.m. (Japan Standard Time)
Video from the presentation will be available on-demand after the livestream.
*Livestream link to be shared on this page closer to the date of the event – stay tuned!
About Toyota Motor Corporation
Toyota Motor Corporation works to develop and manufacture innovative, safe and high-quality products and services that create happiness by providing mobility for all. We believe that true achievement comes from supporting our customers, partners, employees, and the communities in which we operate. Since our founding over 80 years ago in 1937, we have applied our Guiding Principles in pursuit of a safer, greener and more inclusive society. Today, as we transform into a mobility company developing connected, automated, shared and electrified technologies, we also remain true to our Guiding Principles and many of the United Nations' Sustainable Development Goals to help realize an ever-better world, where everyone is free to move.
SDGs Initiatives: https://global.toyota/en/sustainability/sdgs/
About Woven by Toyota
Woven by Toyota is the mobility technology subsidiary of Toyota Motor Corporation. Our mission is to deliver safe, intelligent, human-centered mobility for all. Through our Arene mobility software platform, safety-first automated driving technology and Toyota Woven City — our test course for advanced mobility — we're bringing greater freedom, safety and happiness to people and society. You can learn more about our work at woven.toyota .
MEDIA CONTACT Olivia Boisineau-Beckett [email protected] 734-834-0885
View original content to download multimedia: https://www.prnewswire.com/news-releases/toyota-to-share-progress-on-woven-city-at-ces-2025-302333043.html
SOURCE Toyota Motor Corporation

Recommended Stories
Toyota company presentation
Toyota company presentation it is based on the company you will get an clear idea about the company Toyota after referring this . Thank you all By AN Read less
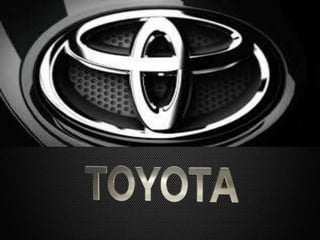
More Related Content
- 2. TOYOTA… • TOYOTA MOTOR CORPORATION : Japanese multinational automotive manufacturer headquartered in Toyota, Aichi, Japan • FOUNDER : KIICHIRO TOYODA • HEADQUARTERS : TOYOTA, AICHI, JAPAN • DATE FOUNDED : August 28, 1937 • Number of employees : 364,445 (as of March31, 2017)
- 3. TILL 2004 CURRENT
- 6. TOYOTA : HEADQUARTERS TOYOTA, AICHI PREFECTURE,JAPAN
- 7. Most valuable brands within the automotive sector worldwide as of 2017, by brand value (in billion U.S. Dollars)
- 8. History From the Very Beginning ...... • Began as a textile company in 1926(Toyoda Automatic Loom Works) • In 1933 an automobile department was established within Toyoda Automatic Loom Works. • In 1937 Toyota Motor Co. was established as an independent company by Kiichiro
- 9. “MR. SAKICHI” Invented Japan's first power loom KIICHIRO TOYODA TOYOTA'S FOUNDER
- 10. • Toyota has become the largest vehicle manufacturer in Japan with over 40% market share • Toyota began to make inroads into foreign markets in the late 1950s. • The company was renamed as The Toyota Motor Co. in 1937.
- 12. In 1951 Toyota first introduced the now world famous Land Cruiser model Toyota focused on the quality of vehicles and gave importance to keep the production costs as low as possible.
- 13. • One of the greatest legacies left by Kiichiro Toyoda: The Toyota Production System. Kiichiro's "just- in-time" philosophy - producing only precise quantities of already ordered items with the absolute minimum of waste - was a key factor in the system's development. • Progressively, the Toyota Production System began to be adopted by the automotive industry across the world.
- 14. TOYOTA PRODUCTION SYSTEM • Toyota Production System (TPS) is one of the most productive, efficient and beautiful management systems ever designed. • It is a socio technical system developed by Toyota which integrates theory with practice. • TPS is one of the most successful production system (or methodology).
- 15. THE MAIN OBJECTIVES OF THE TPS • 1) To reduce waste • 2) To have minimal inventory through JIT(just-in-time) • 3) To have lean manufacturing system
- 16. TOYOTA PRODUCTION SYSTEM HOUSE
- 17. • Just In Time (JIT) - Making only what is needed, when it's needed, and only as much as is needed. • Jidoka - Building quality into the production system and ensuring damaged parts do not proceed to the next stage.
- 19. TOYOTA’S OPERATIONS MANAGEMENT
- 20. DESIGN OF GOODS AND SERVICES VOLUME OF OUTPUT VARIETY VARIATION VISIBILITY The operational process of Toyota The operational processes of Toyota can be categorized into four categories : 4 Vs
- 22. Quality Management • Toyota adopts a flexible capacity production approach in its TPS to achieve efficiency across its supply chain. • This is considered to be a global methodology benchmark of efficiency. • This method is based on the concepts of Jidoka and JIT. • Both are focused upon meeting demand through perfect quality while lowering inventories and waste elimination.
- 23. • Toyota uses TQM for improving the quality of work and processes and to support people working for the organization • Toyota’s quality control in production ensures that right materials and parts are used and also ensures that parts are fitted with precision and accuracy. • This effort is combined with many other rigorous inspections which are performed by team members in the production process.
- 24. Experiencing extreme heat and cold in a day REFREEZING INSOLATION TEST
- 25. Collision tests Vehicle Inspection Under The Glass Pit Dummy Setting
- 26. For every road in the world Flooded Road Driving Test Rubblestone Road Test
- 28. Process and Capacity Design OPERATION DESIGN PROCESS ANALYSIS Toyota uses segmented assembly lines with one piece flow production workstations and as a result delivery times have been shortened. LAYOUT DESIGN Work cell layout is used by Toyota for production efficiency. They focus on assembling of parts so that the layout assembles fabricated parts together suing many different machines that are arranged around the production line).
- 29. CAPACITY PLANNING • Capacity means ability to fulfill the demand of customers • Toyota set its production capacity at the minimum demand levels and meet the increase in demand through overtime and through the use of excess machine capacity and hiring of temporary workers
- 30. LOCATION STRATEGY OF TOYOTA • Toyota is a global producer of automobiles and their components. • Toyota has positioned itself at the most central locations . • In next three years Toyota Company aims to achieve the 35% of market share.
- 31. • Toyota uses global, regional and local strategies. For example, the company has localized manufacturing plants in the United States, China and Thailand, as well as official dealerships in all markets except Mongolia and some countries in the Middle East and Africa. • Thus, Toyota addresses this strategic decision area of operations and management through a mixed set of strategies
- 33. • Toyota's overseas business has evolved through three stages: efficient global production and supply. increasing investment so as to boost production capacity. They began production of the Fortuna in India in 2009, followed by the diesel Corolla and the Etios in 2010, and expanded investment in factories accordingly.
- 34. • In Brazil, production of the Corolla FFV began in 2007, and sales have steadily increased since then. • As a result of such efforts, production capacity in emerging markets is forecast to reach approximately 3.1 million vehicles in 2013
- 35. Localization Initiatives • Toyota believes that ensuring cost competitiveness by achieving thorough localization is necessary to making further progress in intra- and extra-regional exports. Therefore they are maximizing local R&D functions, and seek to achieve local/ regional procurement rates of 100% at the earliest possible stage.
- 36. LAYOUT DESIGNB AND STRATAGIES OLD STANDARD LAYOUT FOR TOYOTA PLANTS • Traditionally, Toyota assembly lines consisted of three to four sub- lines, each about 300 meters in length. The trim line is for the installation of electrical parts. In the chassis line, the drive train, motor, exhaust, etc., are added. During the final line, bumpers, window glass, wheels, etc., are attached. LAYOUT EXPERIMENTS AT THE KYUSHU PLANT 1992 • For the new Kyushu plant constructed in 1992, this division was increased significantly. The line was split into a total of eleven self-contained subsections. Each section is about 100 meters long.
- 37. Changes in the Motomachi Plant 1994 • In 1994, the Motomachi line was also renovated. While not as radical as in Kyushu, some of the longer segments were split into smaller parts (one trim, two chassis, two final). Below is the 1994 layout of the Motomachi line:
- 38. New Layout Motomachi Plant • Below is the current (2014) layout of the Motomachi plant. Compared to the previous layout from 1994, this one contains many more individual segments divided by small buffer stocks (green boxes). • With eight line segments, the plant still has less than Kyushu in 1992 (eleven segments), but more than in the 1994 renovation (six segments) and much more than before 1994 (three to four segments). • Each small blue box below represents one station along the line or, in most cases, approximately one worker (not counting team and group leaders).
- 39. • The exact number of people in the line depends also on the customer demand. One of the methods to adjust the output of the line is by adding or removing workers. • When I observed the line, I measured a cycle time of 2:20 minutes per vehicle. The highly automated welding line was much faster, being able to produce one chassis in just over one minute.
- 40. • Interestingly, rather than cramming the line full with chassis (the Western way), Toyota used a pull system. • New chassis were released only at the speed at which the assembly line could take them, hence there were always idle stations without any chassis in the welding line.
- 41. CURRENT LAYOUT OF TOYOTA MOTOMACHI PLANT
- 42. JOB DESIGN AND HUMAN RESOURCEJOB DESIGN • Job Design is the process of structuring work and designing work for the specific job in Toyota. Job design gives the answers to basic questions of how the job is performed, who is to perform. • In Toyota's working environment most jobs have high job scope. In a job with less scope, jobholder has to performed few tasks. • Job depth refers to the freedom of the job holders to plan and organize their own work.
- 43. How Toyota can maintain employee's satisfaction and low employee's turnover There are different techniques which are used to make employee satisfied and ultimately low employee's turnover which are: • HR Development • Career Development • Motivation
- 44. HR DEVELOPMENT • Skills and knowledge of staff is crucial for Toyota's innovation process. Most of the innovation ideas are come through the employees of the Toyota Motor. • But the time is changing so quickly that every technology and change becomes obsolete in no time. • It is important for the Toyota that its employees remain up-to-date with the knowledge and changes to compete in the industry
- 45. CAREER DEVELOPMENT • It is the duty of the Toyota's management to provide the growth opportunities to its employees. It is also the responsibility of the Toyota's employee himself to think about his career development. • Toyota also helps, guide and provides opportunities to its employees.
- 46. MOTIVATION • Motivation is a feeling of satisfaction and commitment towards its goals and objectives. • This is an internal psychological state which determines the action of the person. Toyota enhances its employee's motivation through two basic ways: 1. Financial: salary system, bonuses, and allowances etc. 2. Non- financial: honors, self respect
- 47. SUPPLY CHAIN MANAGEMENT • Supply-chain management at Toyota is an element of company’s operations strategy which is thoroughly based on the Toyota Production System (TPS). • It was developed in the 1940’s by Shigeo Shingo and Taiichi Ohno. • The principles of which is expressed by the term of “lean manufacturing” • Lean Concept” Lean philosophy aims to elimination of all waste, superior customer care and Lean is based on pull system where the elimination of waste seen as a primary objective.
- 48. LEAN MANUFACTURING The concept of lean manufacturing originates in the Toyota Motor Corporations; resulted from scarcity of resources and intense domestic competition in automobile market in Japan. The lean philosophy incorporated the JIT production system and the Kanban method of pull production
- 49. • Studies show that lean manufacturing reduces human effort by 50% along with the manufacturing space, tool inventory and improved financial performance • The lean production system requires rapid flows of information along the value chain. • Toyota uses the Kanban system to achieve this along with computerised information that can be exchanged with the suppliers to reduce lead times
- 50. KAIZEN • A central tenet of lean production is the concept of kaizen that is continuous improvement in the production process • The concept of Kaizen seeks to remove all activities that do not add value, referred to as “waste” or “muda” in Japanese. • The concept of Kaizen ensures that all employees are quality conscious and focuses on quick problem solving. • The Kaizen empowers the employees and seeks new methods of work. • All employees have are trained to develop the knowledge and skills needed for quality production
- 51. Toyota’s seven major types of non-value-adding waste in business and manufacturing business is shown by Liker (2004, pp.28-29) in he suggests eighth’s type as well
- 52. THE SEVEN WASTE 1. Overproduction: Producing more than the demand for customers resulting in unnecessary inventory, handling, paperwork, and warehouse space. 2. Waiting Time: Operators and machines waiting for parts or work to arrive from suppliers or other operations. 3. Transportation: Double or triple movement of materials due to poor layouts, lack of coordination and workplace organization. 4. Processing: Poor design or inadequate maintenance or processes requiring additional labour or machine time.
- 53. 5. Inventory: Excess inventory due to large lot sizes, obsolete items, poor forecasts or improper production planning. 6. Motion: Wasted movements of people or extra walking to get materials. 7. Defects: Use of materials, labour and capacity for production of defects, sorting our bad parts or warranty costs with customers.
- 54. OBJECTIVES OF LEAN ARE: • To have only the required inventory when needed • To improve quality to zero defects • To reduce lead times by reducing setup times, queue lengths, and lot sizes. • To incrementally revise the operations themselves • To accomplish these things at minimum cost”. • Identifying and eliminating non-value-adding activities, • Employing teams of multi-skilled workers, • Using highly flexible, automated machines” • To do more & more with less & less – Less men, less equipment, less time, less space, less material
- 55. DRIVERS OF SUPPLY CHAIN FACILITY • Vehicles coming out of assembly line are moved into warehouse called “Marshaling yard” . • Fitting accessories, price tag and final quality assurance takes place here. INVENTORY: • Just-in – time based inventory method. • Pull based system and kanban methods are followed.
- 56. TRANSPORT: Majority of transport of raw material through truck , since suppliers stay close to plant. Finished products transported through truck or rail for transport within the country and ships for export. Road transport is provided by third party logistic providers. INFORMATION: Parts and master database is maintained for part name, supplier, lot size information. 13 week forecasting is given to suppliers to provide them with guidance.
- 57. SUPPLY CHAIN OVERVIEW
- 58. SUPPLIERS : • Suppliers provide thousands of parts and components that go into the vehicle. • Toyota organized its suppliers into functional tiers. • The first tier suppliers worked together in a product development team and the second tier suppliers made individual parts. • The first tier suppliers were highly co-operative. There is a high degree of co-operation and information exchange between them. • Since Toyota relies on JIT it has fewer but reliable tier 1 suppliers. Eg : Denso, Bridgestone etc INBOUND LOGISTICS : • Company establish partnership with third party logistic providers • Company organizes many of its suppliers into clusters based on geographic location. • Parts are picked up from those suppliers by trucks on a milk route and delivered to regional cross dock
- 59. • At cross dock, parts are unloaded and staged for each assembly plant and then loaded to trucks which take parts directly to each plant. • After the parts are unloaded, the truck is reloaded with the corresponding empty returnable containers. • Returnable containers flow in reverse route INBOUND LOGISTICS PLANNING –STEPS
- 60. PRODUCTION • Vehicles are produced at the final assembly plant from the parts provided by hundreds of suppliers. • The plant is subdivided into shops. The vehicle is born in the body shop where the frame and body are formed. • The body parts are stamped in the stamping shop by presses. • The body shop is where numerous robots are used to weld the body parts together. • After body being assembled, it moves to paint shop • After painting ,it moves to final line where supplier parts are installed to make finished vehicle. • Final Inspection is done and moved to yard.
- 61. Dealers : • responsible for selling the vehicles produced by the manufacturer to the retail customers. • Toyota s sales model is designed so that a high percentage of vehicles is sold from a relatively low level of dealer stock. Outbound logistics
- 63. JIDOKA(MEANING ‘AUTONOMATION’)- • Jidoka (meaning ‘autonomation’)-a term used in Lean manufacturing meaning "automation with a human touch." • Toyota has deployed the “Semi Automation” Jidoka that maintains a balance between the machines and humans. • The automation in this production system is in line complies with the continuous improvement paradigm that constantly identities and eliminates any problems in the production process. • This is more economical and makes the production process, more flexible. • The lean approach for automation includes low cost equipment and tools that are reused for new models
- 64. JUST-IN-TIME (JIT) INVENTORY MANAGEMENT • Just In Time is a management strategy based on planned elimination of all waste and continuous improvement of productivity. That is “the right material, at the right time, at the right place, and in the exact amount”. • A production process is said to be Just-In- Time when it uses the raw materials to make the good or service after the product has been ordered. • Actually it is pioneered by Toyota. In fact, a Toyota engineer coined the term itself.
- 65. JUST-IN-TIME BENEFITS • This strategy helps companies lower their inventory carrying costs, increase efficiency and decrease waste. • Employees who possess multiple skills are utilized more efficiently. • Total Quality Management, elimination of waste, • Reducing inventory through involving suppliers in planning process, • continuous improvement, improving machinery and focusing on co-operation. • The JIT systems become more efficient and used the Kanban as an information exchange tool for different production lines • In 1959 Toyota dramatically increased its productivity and produced 100,000 cars for the first time
- 66. KANBAN • Kanban “sign board" or “bill board," is a concept related to lean and just in time (JIT) production. • Kanban is not an inventory control system; it is a scheduling system that helps determine what to produce, when to produce it, and how much to produce. • The need to maintain a high rate of improvement led Toyota to devise the Kanban system. • Kanban became an effective tool to support the running of the production system as a whole.
- 67. Kanban System • The Kanban system uses simple cards or signals to strictly control production .Kanban each part travels with a card. • New stock will only be required when that part has been used, the card is removed, using signals to re- stock this part. • Kanban is well integrated in Toyota’s production system, because in Toyota there are limited number of parts with stable demand for them. • The Kanban system ensues that there is no waste of overproduction and the inventory costs are reduced
- 68. • https://www.youtube.com/watch?v=FkVJ5no4 UlA
- 69. TOYOTA PRODUCTION SCHEDULING • The production schedule is created once a month from the sales order and forecast. • sales divisions submit a rolling three-month order and forecast each month. • The Production Control division must create a daily production plan to execute the agreed-upon schedule.
- 70. SCHEDULING PROCESS • The first step in creating the production schedule is to use the sales order and forecast data to create individual records for each vehicle and assign a unique reference number. • This step is necessary because each vehicle has to be assigned to a production slot.
- 71. • The Vehicle Identification Number (VIN) can be used to identify a unique vehicle, the VIN is not assigned until the vehicle is started in the body shop. • Therefore, a Unique Reference Number (URN) is assigned to identify vehicles prior to production line-off.
- 72. HEIJUNKA (OR SMOOTHING) • Heijunka (or smoothing) is a technique to avoid supply chain congestion, workload imbalance, inventory batching, and the like. • A Heijunka process is used to schedule the vehicles by day, by line, by plant
- 73. • Some sales orders have specific build dates requested, so those orders need to be scheduled first • The remaining orders are grouped by build combinations and spread throughout the month so that the number of identical orders will be evenly distributed across the month. • The destination of vehicles is also considered as one of the heijunka factors because it is important to have an even flow of vehicles to each region • The heijunka process is completed, then each order is assigned the scheduled production day. • This production schedule is then sent back to the sales division to advise its members of each vehicle’s Unique Reference Number.
- 74. TOTAL PRODUCTIVE MAINTENANCE • Total Productive Maintenance A main pillar of the Toyota Production System (TPS) is Total Productive Maintenance (TPM). • The essential strategy is to eliminate the potential of a problem. • That is, eliminate a problem before it occurs.
- 75. TOTAL PRODUCTIVE MAINTENANCE Basic Elements: 1. Maximizes equipment effectiveness. 2. Establishes a through system of preventative maintenance (PM) for the equipment`s entire life span. 3. Implemented by various departments (engineering, operations, maintenance). 4. Involves every single employee- from top management to workers on the floor. 5. Based on the promotion of productive maintenance through workforce motivation management via autonomous small group activities.
- 76. THE GOAL OF TOTAL PRODUCTIVE MAINTENANCE • To achieve overall equipment effectiveness, TPM works to eliminate the six big losses that are formidable obstacles to equipment effectiveness: • DOWN TIME: 1. Equipment failure - from breakdowns. 2. Setup and adjustment - from exchange of die in injection molding machines, etc.
- 77. SPEED LOSSES: 3. Idling and minor stoppages - due to the abnormal operation of sensors, blockage of work, etc. 4. Reduced speed - due to discrepancies between designed and actual speed of equipment. Defects: 5. Process defects - due to scraps and quality defects to be repaired. 6. Reduced yield - from machine start-up to production stability.
Editor's Notes
- https://youtu.be/P-bDlYWuptM
- https://youtu.be/ehSWGOLqRmU
- 2.where it has clear and very optimistic control over the company's products and their delivery to customers

COMMENTS
Oct 29, 2015 · Toyota Philosophy; Guiding Principles at Toyota; Toyota Way 2020 / Toyota Code of Conduct; Toyota Global Vision; Toyota Production System; Toyota Group Vision
Presentation by Koji Sato, President & CEO, Member of the Board of Directors. At the Japan Mobility Show 2023, Toyota unveiled an inspiring vision for the fu...
Sep 6, 2023 · Presentation by Simon Humphries. Good afternoon, everyone. Today marks a special moment for a car at the very pinnacle of the Toyota portfolio―Century. Century is a singular automobile representing the height of Japanese sensibilities. Born as the pride of Toyota, Century has become the pride of Japan. It takes a nation to build a Century.
Apr 14, 2023 · This presentation focuses on Toyota's efforts to transform itself into a mobility company. Apr. 14, 2023 Accelerating the shift to a Mobility Company: President Sato Talks about Toyota's Future
3 days ago · Toyota to Share Progress on Woven City at CES 2025 December 16, 2024 TOKYO (Dec. 17, 2024) ―Toyota Motor Corporation announces that it will return to CES 2025 with plans to make a presentation on Woven City during Media Days on January 6, 2025 starting at 1:00 p.m. Pacific Standard Time.
2 days ago · Toyota Motor Corporation announces that it will return to CES 2025 with plans to make a presentation on Woven City during Media Days on January 6, 2025 starting at 1:00 p.m. Pacific Standard Time.
Sep 20, 2014 · Introduction On Toyota Motors Toyota is 3rd largest automotive manufacturer Toyota Motor Corporation is headquartered in Toyota City, Aichi Toyota has annual sales of $120 Billion Produces ~5.5 million vehicles per year From 56 manufacturing plants across 6 continents Employs ~ 325,905 (as of March 31, 2013) Headquarter of Toyota City, Aichi-Japan
Apr 21, 2014 · Toyota is a Japanese automotive manufacturer headquartered in Toyota City, Japan. It was founded in 1937 by Kiichiro Toyoda and is now the largest automaker in the world by production. In 2013, Toyota employed over 333,000 people worldwide and had annual revenue of over $200 billion.
Jan 27, 2019 · 23. • Toyota uses TQM for improving the quality of work and processes and to support people working for the organization • Toyota’s quality control in production ensures that right materials and parts are used and also ensures that parts are fitted with precision and accuracy.
Toyota Motors is the 3rd largest automotive manufacturer that produces over 5.5 million vehicles annually. The presentation summarized Toyota's history, founding in 1937, key leaders, business segments including automotive and financial services. It also described Toyota's production system focusing on lean manufacturing and just-in-time principles. Additional topics covered Toyota's global ...